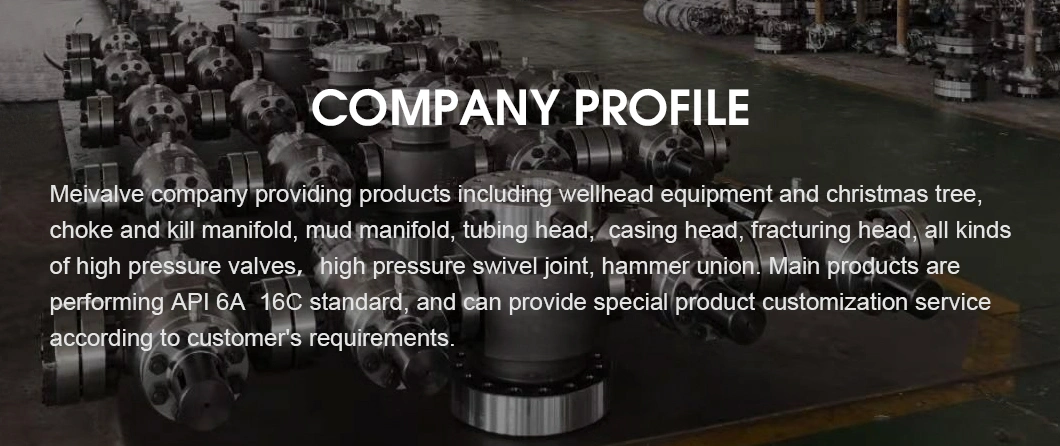

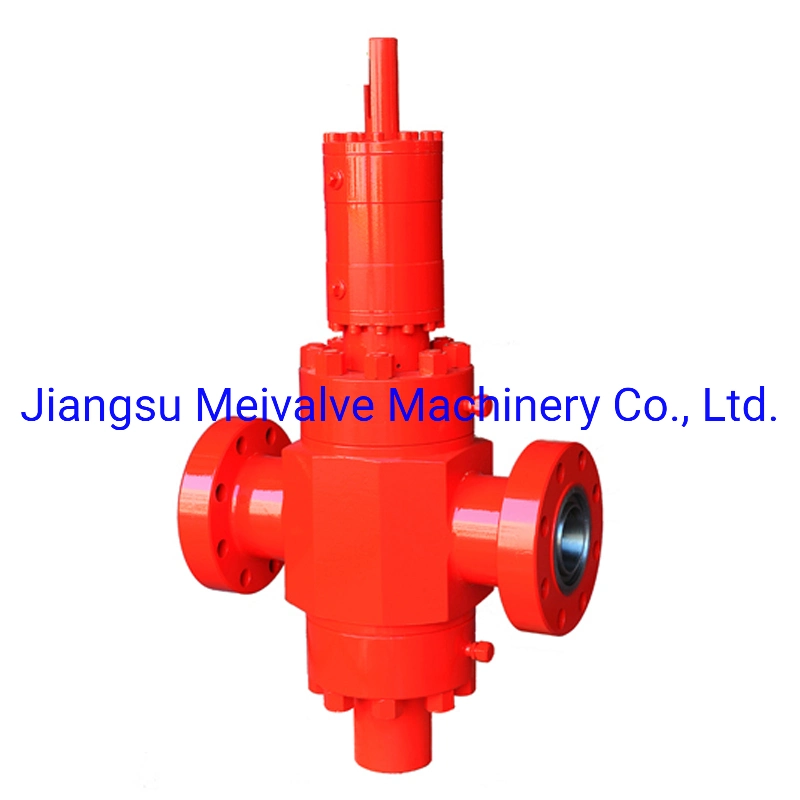
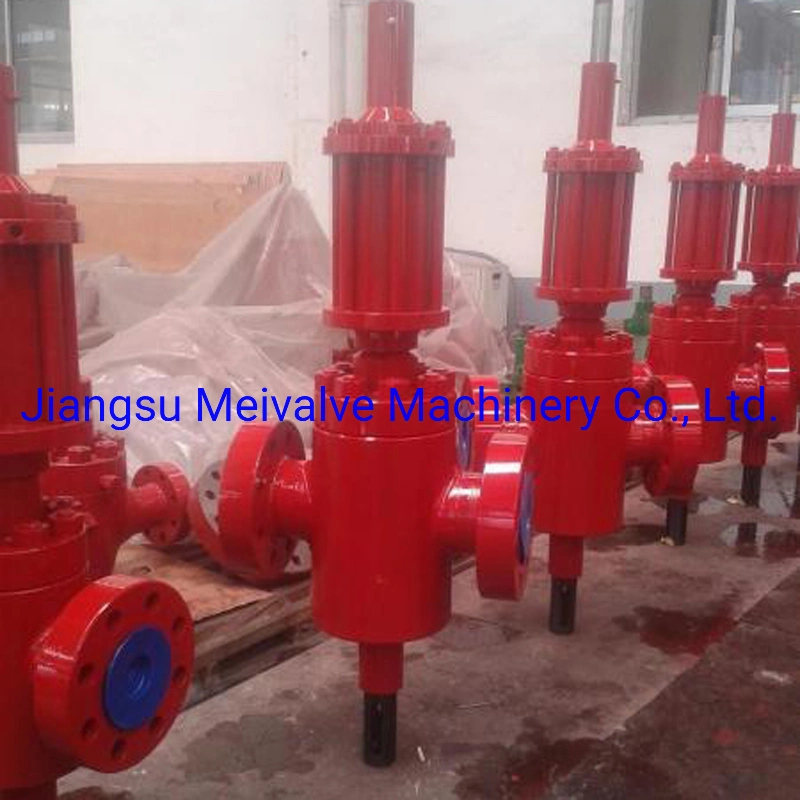
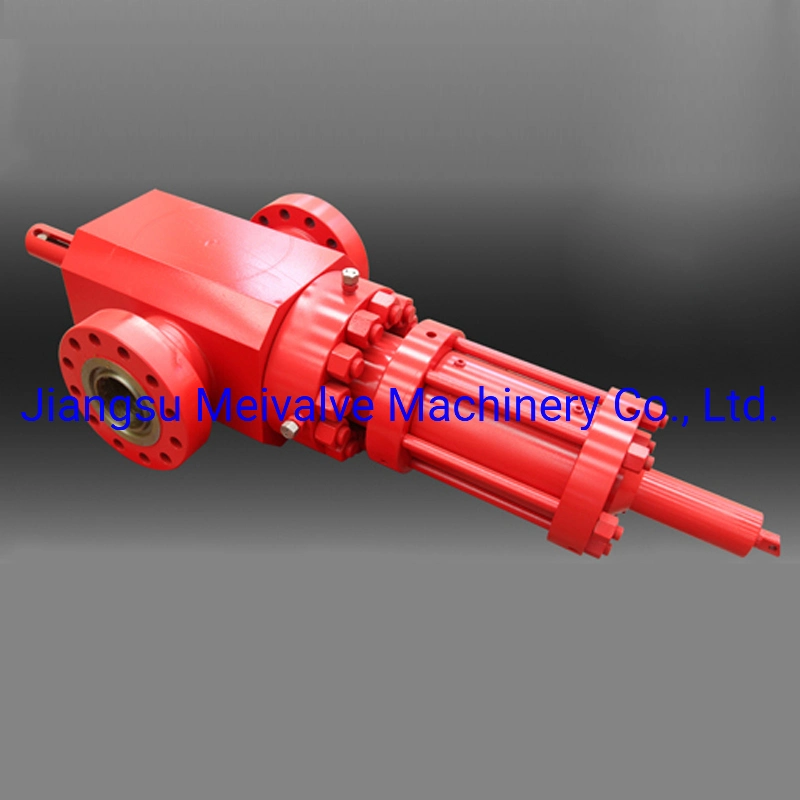
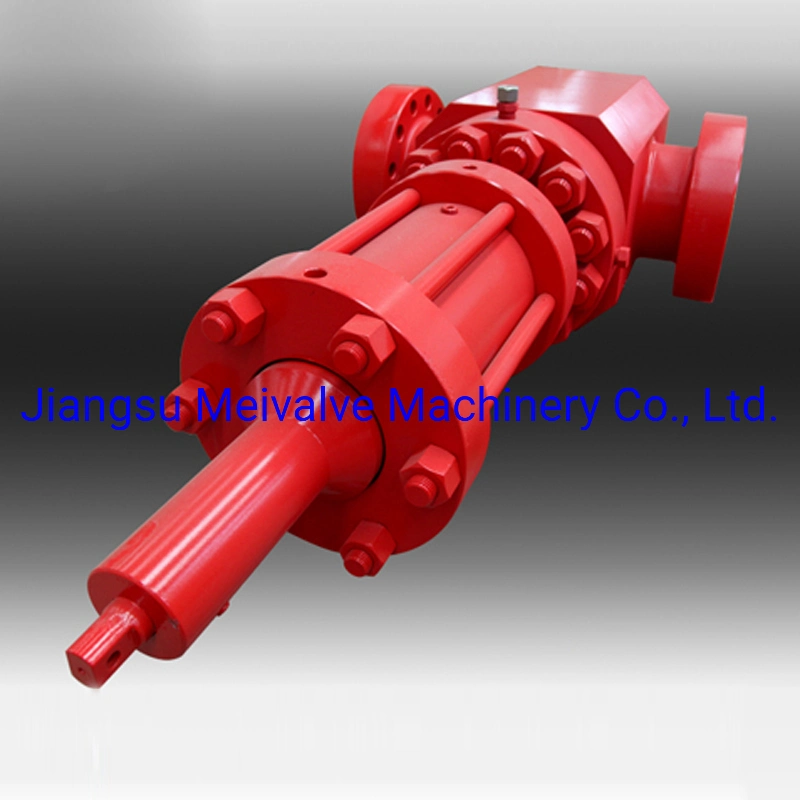
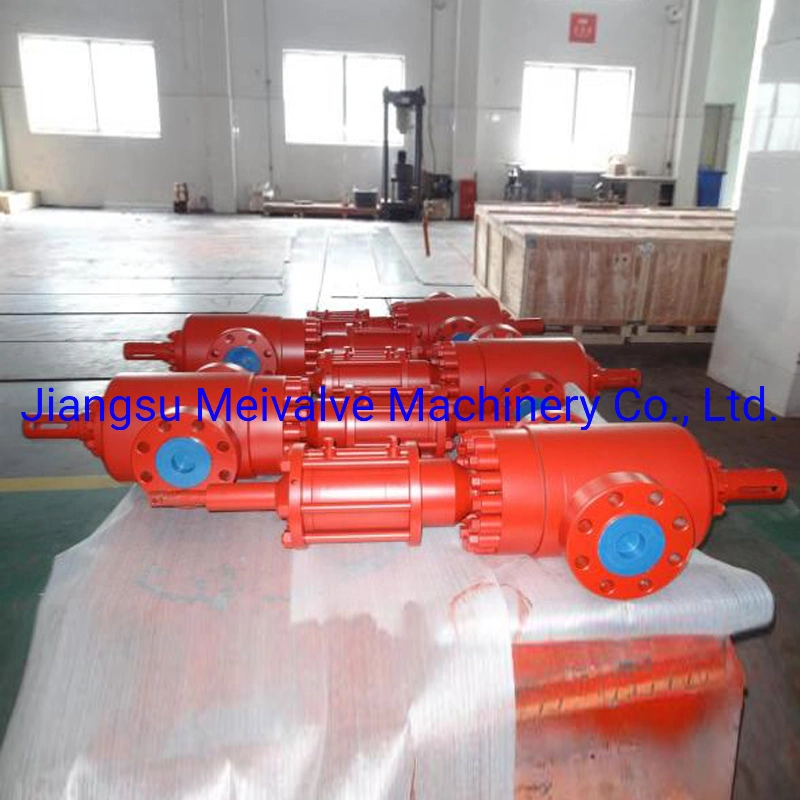
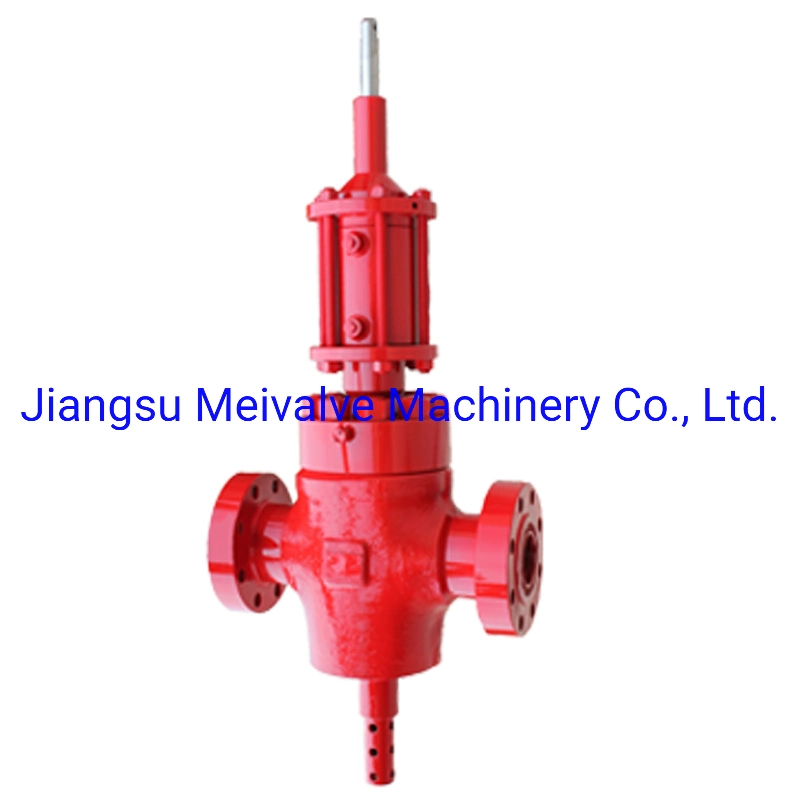

1.Designed, manufactured and tested in Accordance with API Spec. 6A.
2.Linear double acting actuators guarantee opening valves rapidly in 30 seconds
3.Integrally forged valve body,The sealing surface of the gate are sprayed by carbide alloy at high velocity and seats are made of carbide alloy to enhance wear resistance, corrosion resistance and service life
4.Gate to seat, seat to body, bonnet seal and stem backseat are metal to metal sealing
5.The gate valve is fitted with a balancing lower stem to work with a double acting hydraulic actuator to provide positive, reliable control through the entire stroke of the valve. Should a failure of hydraulic power occur, this valve will remain in position.
6.Double acting actuator that requires hydraulic power to both open and close, providing positive control during operations
7.Balancing stem that allows gate to stay in position unless hydraulic power is supplied to actuator to positively open or close valve
8.Two spring-loaded, pressure-energized, nonelastomeric lip seals between each seat and body, which assist in low-pressure sealing and protect against intrusion of particle contaminants into the body cavity and seal areas
9.Stem seal design that covers a wide range of pressures, temperatures, and fluids encountered in wellhead and manifold service Metal-to-metal bonnet seal
10.Manual locking screw that maintains the gate (valve) in the closed position without any operating pressure in the actuator
11.Use of socket head cap scre ws to tie down actuator head flanges, reducing area exposed to corrosive environments

1.Medium: oil and gas accompanied with sour gas or / and sand
2.Hydraulic actuator: 3,000 psi working pressure and 1/2" NPT connection
3.Rated Working Pressure: 5,000psi ~ 20,000psi
4.Bore Size: all popular
5.Temperature: K ~ U
6.Material Classes: EE ~ HH
7.End connections: flange
8.Product Specification Level: PSL1 ~ PSL3
9.Performance Requirement: PR1, PR2
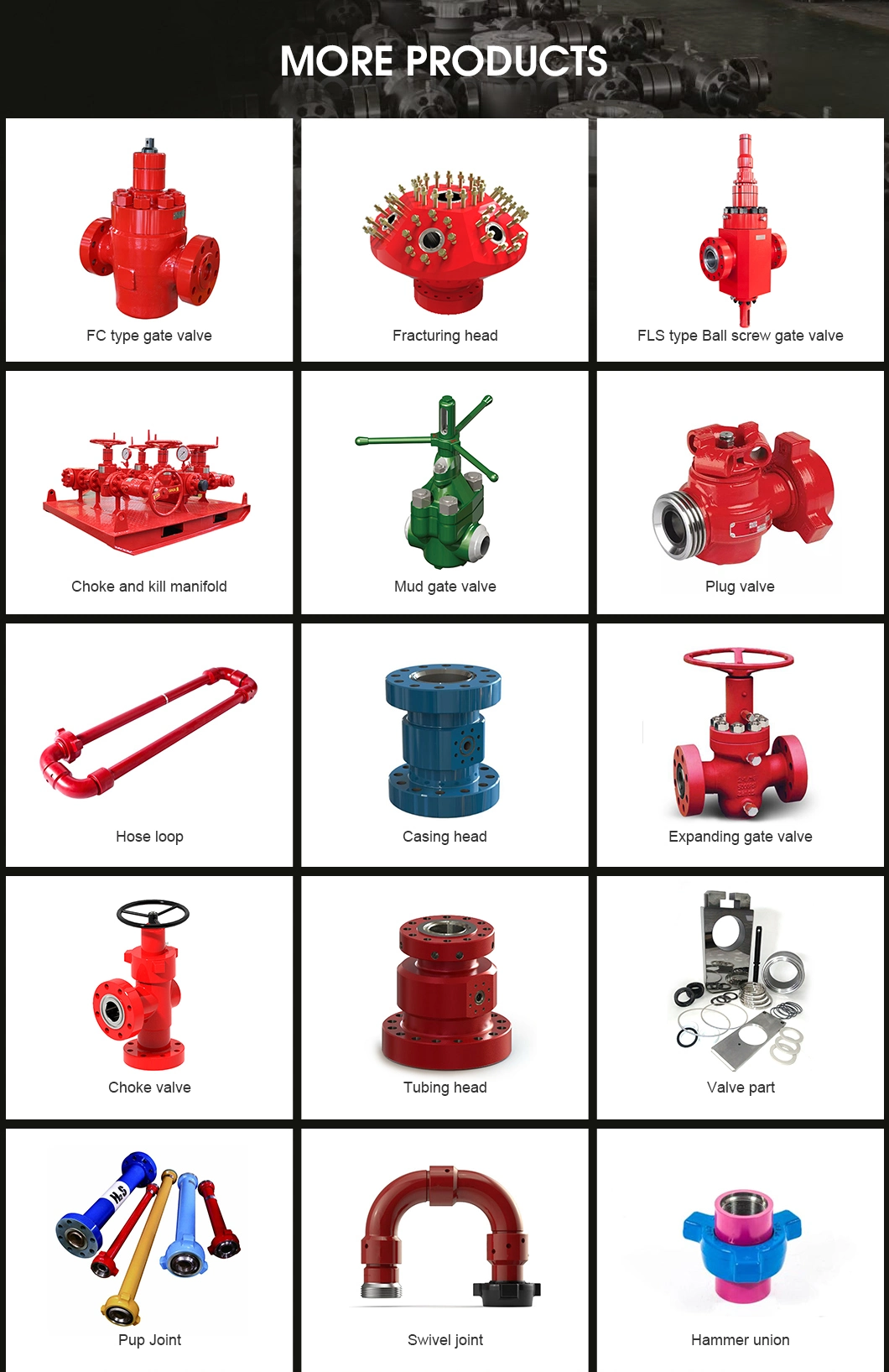
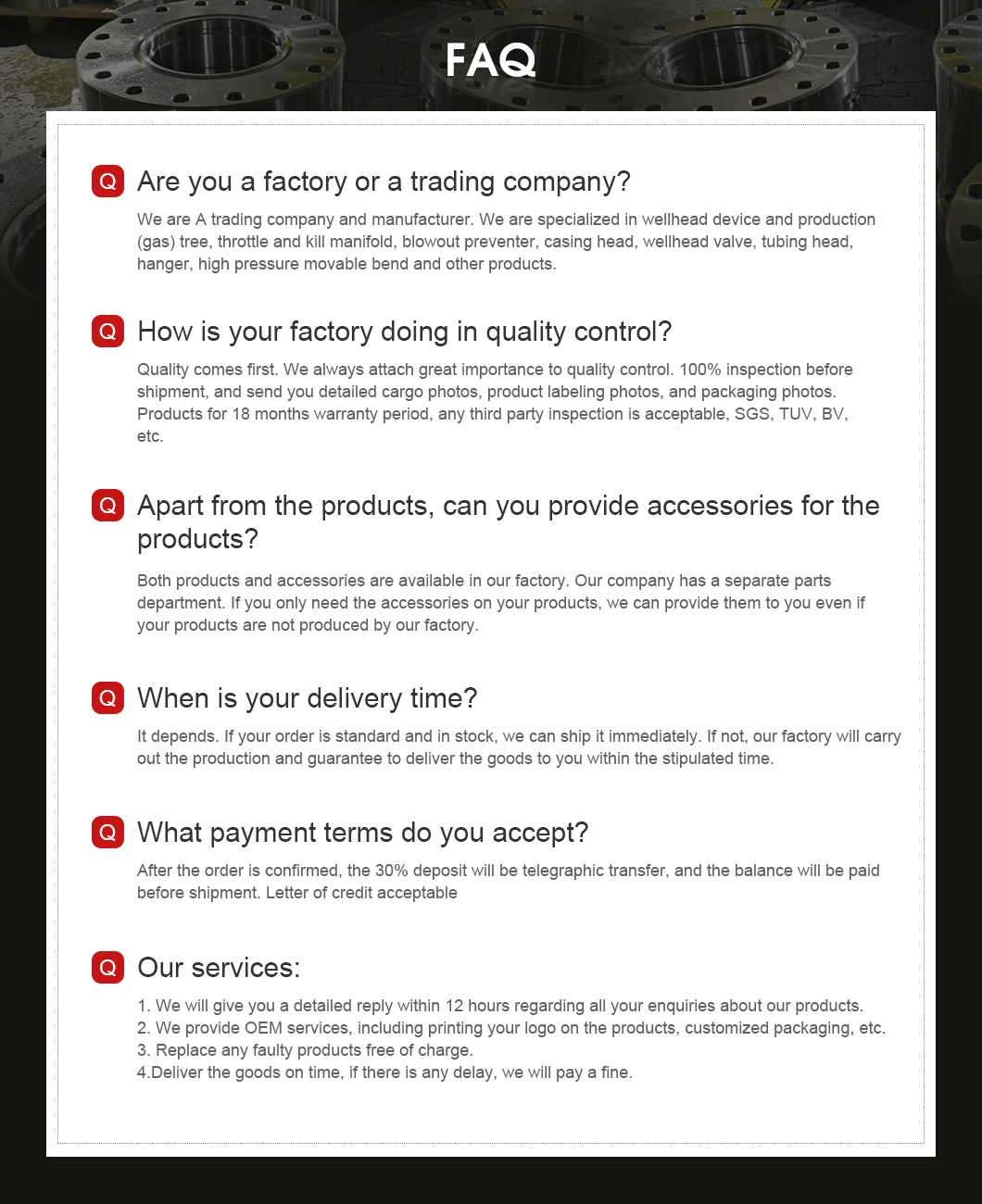